Prefabricated Sump Proposal and Trial
MWH Constructors
May 2016 - July 2016
After my second year at the University of Colorado, I was eager to put my new found engineering skills to use in a professional environment. I was fortunate enough to be able to do so in the United Kingdom. Working in an MWH Constructors joint venture called the @One Alliance, I worked to create a proposal for a new construction method.
Traditionally, in the @One Alliance, sumps were formed out of concrete and rebar. While this method has low material cost, it requires a significant amount of man hours as multiple concrete pours are needed. The alliance focuses on reducing time on site as it in turn helps to reduce injures and cost. To make improvements to the sump, I looked into using a prefabricated version that could be installed with a single concrete pour. To have the prefabricated sump be an effective tool for the @One Alliance, the design needed to be simple to install, usable in many applications without modification, and cost less than the existing method.
For this project, the design iteration process was relatively short. I ended with a stainless steel sump the was comprised of three separate components. Tubing was used for the side walls of the sump to reduce the weld count as compared to a rectangular sump, metal sheeting was used to seal the tube at the bottom, and a flange was added on the side to prevent water from getting underneath the sump. To gain further insight into the fabrication process, I traveled to the manufacturer who would be building these sumps to make one myself. By discussing some potential cost saving changes to the design and how to optimize usage of the metal stock, we were able to reduce the estimate cost of larger scale production runs.
The most important part of this project was the trial of the prefabricated sump. I needed to prove that the use of this method would provide substantial time savings. During this trial, it was found that the labor time was reduced by 80%. This time savings offset the increased material cost, resulting in a 34% cost reduction. Over a standard 5 year planning period that the @One Alliance uses, an estimated £44,000 could be saved.
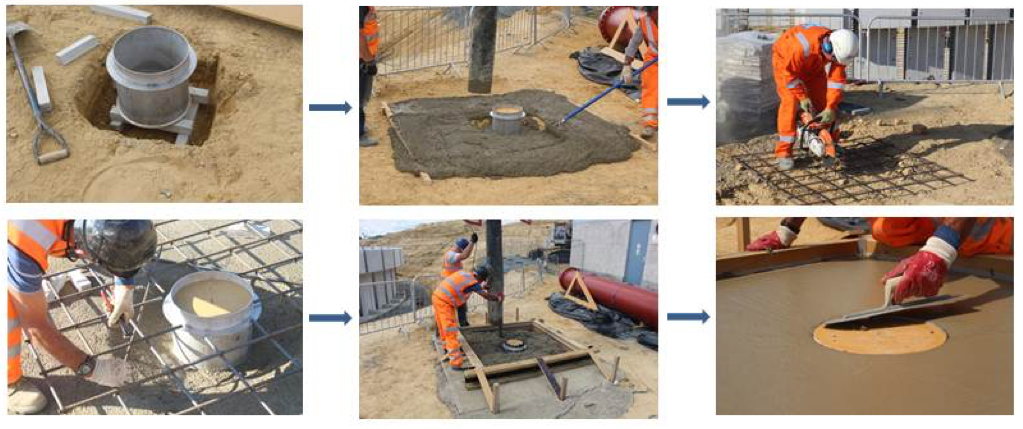